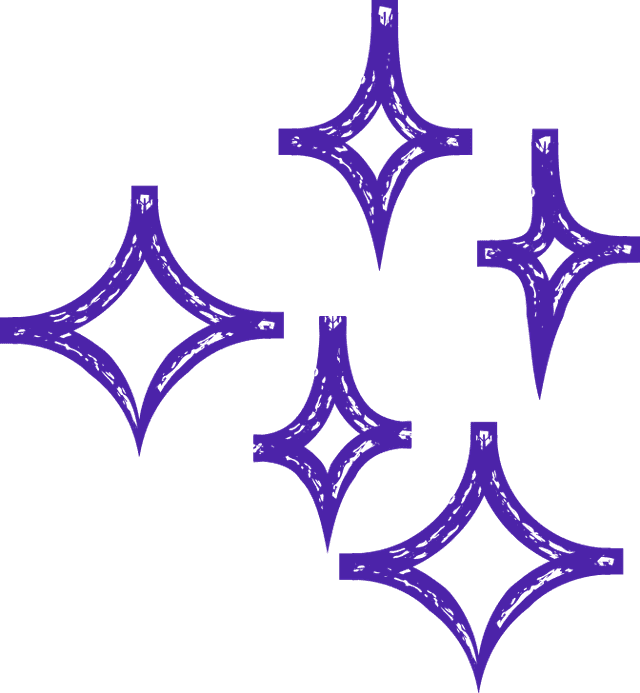
root cause
Root Cause Analysis: Uncovering the Source of Problems
In various fields, including engineering, business, and quality management, root cause analysis (RCA) is a valuable technique employed to identify and address the underlying causes of problems or failures. It is a systematic approach that delves beyond the symptoms to uncover the root cause, helping to prevent recurrence and drive continuous improvement.
The purpose of root cause analysis is to go beyond treating symptoms and instead focus on identifying the fundamental reasons for problems or failures. By understanding the root cause, organizations can implement targeted corrective actions that address the underlying issues, rather than simply applying quick fixes. Root cause analysis involves a structured and analytical process, aiming to answer the question: "Why did this problem occur?" It's like peeling back the layers of an onion to uncover its core.
There are various methodologies and techniques for conducting root cause analysis, including the "5 Whys," fishbone diagram (Ishikawa diagram), fault tree analysis, and Pareto analysis. The "5 Whys" technique involves asking "why" repeatedly to dig deeper into the causes of a problem. The fishbone diagram helps identify potential causes by categorizing them into various dimensions, such as people, process, equipment, or environment. Fault tree analysis is a graphical method that explores different events and combinations of events that could lead to the problem. Pareto analysis prioritizes potential causes based on their frequency or impact, helping to focus efforts on the most significant contributors. Each technique has its strengths and is chosen based on the nature of the problem and available data.
Root cause analysis plays a significant role in preventing problems from recurring and driving continuous improvement. By addressing the underlying causes, organizations can implement effective corrective and preventive actions to eliminate or minimize the likelihood of similar issues in the future. This leads to increased reliability, efficiency, and customer satisfaction. Root cause analysis also provides valuable insights into process inefficiencies, organizational weaknesses, or systemic issues that need to be addressed. It helps foster a culture of continuous improvement, where problems are viewed as opportunities for learning and growth. It's like putting on detective hats and investigating the mysteries behind problems.
Conducting a root cause analysis requires a collaborative and multidisciplinary approach. It involves gathering relevant data, analyzing information, and engaging subject matter experts or stakeholders who have firsthand knowledge of the problem. It is important to create a safe and blame-free environment that encourages open and honest discussions. Root cause analysis should be performed with a focus on learning and improvement rather than assigning blame to individuals. Effective communication and documentation of the analysis results are crucial to ensure that corrective actions are implemented and knowledge is shared across the organization.
In conclusion, root cause analysis is a valuable tool for uncovering the source of problems and driving continuous improvement. By identifying and addressing the root causes, organizations can prevent problems from recurring and promote a culture of learning and growth. So, let's embrace the power of root cause analysis to uncover the underlying issues and pave the way for more robust and efficient systems.
Fun fact: Did you know that root cause analysis has its origins in the field of industrial engineering and quality management? It was initially developed by Dr. Kaoru Ishikawa, a Japanese quality management expert, in the 1960s. Since then, root cause analysis has been widely adopted and adapted in various industries and disciplines, proving to be an invaluable approach for problem-solving and continuous improvement.
"A problem well stated is a problem half-solved." - Charles F. Kettering
The purpose of root cause analysis is to go beyond treating symptoms and instead focus on identifying the fundamental reasons for problems or failures. By understanding the root cause, organizations can implement targeted corrective actions that address the underlying issues, rather than simply applying quick fixes. Root cause analysis involves a structured and analytical process, aiming to answer the question: "Why did this problem occur?" It's like peeling back the layers of an onion to uncover its core.
There are various methodologies and techniques for conducting root cause analysis, including the "5 Whys," fishbone diagram (Ishikawa diagram), fault tree analysis, and Pareto analysis. The "5 Whys" technique involves asking "why" repeatedly to dig deeper into the causes of a problem. The fishbone diagram helps identify potential causes by categorizing them into various dimensions, such as people, process, equipment, or environment. Fault tree analysis is a graphical method that explores different events and combinations of events that could lead to the problem. Pareto analysis prioritizes potential causes based on their frequency or impact, helping to focus efforts on the most significant contributors. Each technique has its strengths and is chosen based on the nature of the problem and available data.
Root cause analysis plays a significant role in preventing problems from recurring and driving continuous improvement. By addressing the underlying causes, organizations can implement effective corrective and preventive actions to eliminate or minimize the likelihood of similar issues in the future. This leads to increased reliability, efficiency, and customer satisfaction. Root cause analysis also provides valuable insights into process inefficiencies, organizational weaknesses, or systemic issues that need to be addressed. It helps foster a culture of continuous improvement, where problems are viewed as opportunities for learning and growth. It's like putting on detective hats and investigating the mysteries behind problems.
Conducting a root cause analysis requires a collaborative and multidisciplinary approach. It involves gathering relevant data, analyzing information, and engaging subject matter experts or stakeholders who have firsthand knowledge of the problem. It is important to create a safe and blame-free environment that encourages open and honest discussions. Root cause analysis should be performed with a focus on learning and improvement rather than assigning blame to individuals. Effective communication and documentation of the analysis results are crucial to ensure that corrective actions are implemented and knowledge is shared across the organization.
In conclusion, root cause analysis is a valuable tool for uncovering the source of problems and driving continuous improvement. By identifying and addressing the root causes, organizations can prevent problems from recurring and promote a culture of learning and growth. So, let's embrace the power of root cause analysis to uncover the underlying issues and pave the way for more robust and efficient systems.
Fun fact: Did you know that root cause analysis has its origins in the field of industrial engineering and quality management? It was initially developed by Dr. Kaoru Ishikawa, a Japanese quality management expert, in the 1960s. Since then, root cause analysis has been widely adopted and adapted in various industries and disciplines, proving to be an invaluable approach for problem-solving and continuous improvement.
"A problem well stated is a problem half-solved." - Charles F. Kettering