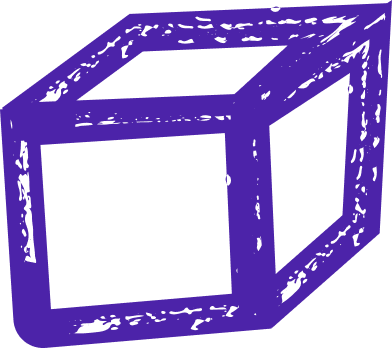
a plc instruction for a normally open input device
Understanding PLC Instructions for Normally Open Input Devices
A Programmable Logic Controller (PLC) is a specialized computer used in industrial automation systems to control and monitor various processes. It is capable of executing a wide range of instructions that enable it to interact with input and output devices. In this context, a PLC instruction for a normally open (NO) input device refers to a specific command or code that is programmed into the PLC to monitor and respond to the status of a NO input device.
Before delving into the PLC instruction, it is crucial to grasp the concept of a normally open input device. In industrial automation, input devices are used to sense and provide information about the state of various parameters such as temperature, pressure, level, or position. Normally open input devices, as the name suggests, are those that are in an open circuit state when not actuated or in their normal position. These devices typically consist of switches, sensors, or other devices that are closed or actuated when a specific condition is met.
PLC instructions are the building blocks of a PLC program, allowing it to perform specific tasks based on the input conditions and control the corresponding output devices. In the case of a normally open input device, a PLC instruction is used to monitor the status of the input and trigger appropriate actions or responses based on the changes in its state.
To write a PLC instruction for a normally open input device, the programmer needs to consider the specific requirements of the industrial process being controlled. The instruction is typically written using a ladder logic programming language, which resembles electrical relay circuits.
The ladder logic diagram consists of rungs that represent the execution sequence of the PLC program. Each rung contains one or more instructions, such as contacts, coils, timers, counters, and other function blocks. In the context of a normally open input device, the ladder logic diagram would include a normally open contact, also known as an input contact.
The normally open contact acts as a virtual representation of the NO input device. It is typically denoted by a horizontal line with a diagonal line running from the left side, indicating the normally open state. When the normally open input device is actuated or closed, the contact in the ladder logic diagram will close, allowing the current to flow and triggering the associated instructions or actions.
Let's consider an example where a PLC is used to control a motor based on the status of a limit switch. The limit switch is a normally open input device that detects the presence of an object. The PLC instruction for this scenario could be written as follows:
1. Start with an empty rung.
2. Add a normally open contact (X1) representing the limit switch.
3. Connect the normally open contact (X1) in series with a coil (Y1) representing the motor.
4. Add a network address to the coil (Y1) to specify the output module or physical output device connected to the motor.
5. Close the rung.
In this example, when the limit switch is actuated or closed due to the presence of an object, the normally open contact (X1) will close, completing the circuit. This closure will energize the coil (Y1), which will, in turn, activate the motor connected to the specified output module.
A PLC instruction for a normally open input device is a vital component of a PLC program that enables the monitoring and control of industrial processes. By understanding the concept of normally open input devices and their role in industrial automation, programmers can write effective PLC instructions using ladder logic. These instructions ensure that the PLC responds appropriately to changes in the status of the normally open input device, facilitating efficient and reliable automation in various industries.
Understanding Normally Open Input Devices
Before delving into the PLC instruction, it is crucial to grasp the concept of a normally open input device. In industrial automation, input devices are used to sense and provide information about the state of various parameters such as temperature, pressure, level, or position. Normally open input devices, as the name suggests, are those that are in an open circuit state when not actuated or in their normal position. These devices typically consist of switches, sensors, or other devices that are closed or actuated when a specific condition is met.
The Role of PLC Instructions
PLC instructions are the building blocks of a PLC program, allowing it to perform specific tasks based on the input conditions and control the corresponding output devices. In the case of a normally open input device, a PLC instruction is used to monitor the status of the input and trigger appropriate actions or responses based on the changes in its state.
Writing a PLC Instruction for a Normally Open Input Device
To write a PLC instruction for a normally open input device, the programmer needs to consider the specific requirements of the industrial process being controlled. The instruction is typically written using a ladder logic programming language, which resembles electrical relay circuits.
The ladder logic diagram consists of rungs that represent the execution sequence of the PLC program. Each rung contains one or more instructions, such as contacts, coils, timers, counters, and other function blocks. In the context of a normally open input device, the ladder logic diagram would include a normally open contact, also known as an input contact.
The normally open contact acts as a virtual representation of the NO input device. It is typically denoted by a horizontal line with a diagonal line running from the left side, indicating the normally open state. When the normally open input device is actuated or closed, the contact in the ladder logic diagram will close, allowing the current to flow and triggering the associated instructions or actions.
Example of PLC Instruction for a Normally Open Input Device
Let's consider an example where a PLC is used to control a motor based on the status of a limit switch. The limit switch is a normally open input device that detects the presence of an object. The PLC instruction for this scenario could be written as follows:
1. Start with an empty rung.
2. Add a normally open contact (X1) representing the limit switch.
3. Connect the normally open contact (X1) in series with a coil (Y1) representing the motor.
4. Add a network address to the coil (Y1) to specify the output module or physical output device connected to the motor.
5. Close the rung.
In this example, when the limit switch is actuated or closed due to the presence of an object, the normally open contact (X1) will close, completing the circuit. This closure will energize the coil (Y1), which will, in turn, activate the motor connected to the specified output module.
Conclusion
A PLC instruction for a normally open input device is a vital component of a PLC program that enables the monitoring and control of industrial processes. By understanding the concept of normally open input devices and their role in industrial automation, programmers can write effective PLC instructions using ladder logic. These instructions ensure that the PLC responds appropriately to changes in the status of the normally open input device, facilitating efficient and reliable automation in various industries.