🌍 All
About us
Digitalization
News
Startups
Development
Design
Mastering Quality by Design: A Practical Guide to Success
Alexander Stasiak
Dec 05, 2024・7 min read
Table of Content
Understanding Quality by Design
Implementing QbD in Practice
Tools and Techniques for QbD
Overcoming Common Challenges
Future of Quality by Design
Quality by Design (QbD) is a proactive approach that focuses on understanding and controlling the process of product development to ensure quality from the outset. This methodology is especially relevant in industries such as pharmaceuticals, where consistent product performance and safety are paramount. By emphasising the importance of design and planning, QbD encourages a thorough examination of each step in the production process, allowing for potential issues to be identified and addressed early on. In this guide, we will delve into practical strategies for implementing QbD, providing insights that are both accessible and actionable for individuals at any proficiency level. Join us in exploring how to achieve success in pharmaceutical development through a structured, quality-focused framework.
Understanding Quality by Design
Origins and Evolution
Quality by Design (QbD) has its roots in the manufacturing sectors, where the focus on improving product quality began to take shape during the industrial revolution. This approach gained significant traction in the 20th century with the advent of quality control theories pioneered by experts like W. Edwards Deming and Joseph M. Juran. Their work emphasised the importance of designing processes that inherently produce desired quality outcomes. In the pharmaceutical industry, QbD gained prominence after the U.S. Food and Drug Administration endorsed it as part of its regulatory guidelines. This move highlighted the need for a systematic approach to product development that prioritises quality from the beginning. Over time, QbD has evolved into a comprehensive methodology that integrates risk management and continuous improvement, providing a robust framework for managing complex processes and ensuring consistent product performance across various industries. This historical context underscores its enduring relevance and adaptability.
Core Principles of QbD
At the heart of Quality by Design (QbD) are several core principles that guide its implementation. First, a deep understanding of the full product life cycle and its processes is essential. This involves identifying the critical quality attributes (CQAs) that affect the final product's safety and efficacy. Secondly, the design of manufacturing processes must be based on scientific knowledge and risk management. This means using data-driven approaches to control variables that impact product quality. Thirdly, a robust control strategy should be developed to ensure consistent product performance. This includes identifying and managing risks throughout the product lifecycle. Additionally, QbD emphasises the importance of continuous improvement, encouraging manufacturers to refine and optimise processes over time. By adhering to these principles, organisations can ensure a proactive approach to quality, reducing the likelihood of defects and ensuring that products meet the necessary standards from the outset.
Why QbD Matters
Quality by Design (QbD) is crucial because it transforms how products are developed and manufactured, ensuring quality is built in from the outset rather than tested at the end. By focusing on understanding processes and identifying potential risks early, QbD reduces the likelihood of defects and recalls, which can be costly and damage reputation. It also enhances efficiency by streamlining production processes, leading to reduced waste and lower costs. For industries like pharmaceuticals, where patient safety is paramount, QbD ensures that products consistently meet stringent quality standards, thus maintaining public trust. Moreover, regulatory bodies increasingly favour QbD approaches, as they provide a more thorough and scientific basis for ensuring product quality. This proactive stance not only improves compliance but also accelerates drug development and time-to-market by reducing the need for extensive post-production testing. Overall, QbD represents a paradigm shift towards smarter, more reliable manufacturing practices.
Implementing QbD in Practice
Identifying Key Processes
A critical step in implementing Quality by Design (QbD) involves identifying key processes that impact product quality. This requires a comprehensive analysis of the entire production cycle to pinpoint stages where variability might affect the final outcome. Begin by mapping the manufacturing process flow, highlighting each step involved in the manufacturing chain. Focus on areas where deviations could compromise the critical quality attributes (CQAs) of the product. This often involves cross-functional teams who can bring diverse perspectives to the table, ensuring all potential risks are accounted for. Techniques such as process mapping and failure mode effects analysis (FMEA) are effective tools for this task. By clearly understanding these key processes, organisations can develop targeted strategies to control variability and mitigate risks. This proactive approach not only ensures a higher standard of product quality but also enhances efficiency and consistency across production, laying a solid foundation for a successful QbD implementation.
Setting Measurable Objectives
Setting measurable objectives is a fundamental aspect of implementing Quality by Design (QbD). Objectives should be specific, quantifiable, and aligned with the critical quality attributes (CQAs) of the product. Begin by defining what success looks like for each process and identify metrics that can track performance against these goals. These metrics could include variables such as yield rates drug quality, defect frequencies, or process times. By establishing clear targets, organisations can focus their efforts on achieving tangible improvements. It's important to ensure these objectives are realistic and achievable, which may require a thorough analysis of current capabilities and potential constraints. Regularly reviewing progress against these objectives allows for timely adjustments and fosters a culture of continuous improvement. Moreover, transparent and consistent measurement helps in communicating progress to stakeholders, ensuring everyone is aligned and committed to the QbD process. Ultimately, well-defined objectives provide a roadmap for achieving high-quality outcomes consistently.
Integrating QbD with Existing Systems
Integrating Quality by Design (QbD) with existing systems can seem daunting, but it is essential for seamless implementation. Begin by assessing current processes and identifying areas where QbD principles can enhance performance. This might involve revisiting standard operating procedures (SOPs) and aligning them with QbD methodologies to ensure they support a proactive quality approach. Collaboration across departments is key, as sharing insights and data facilitates a smoother transition. Additionally, training programmes can play a vital role in equipping staff with the necessary skills and understanding to adopt QbD practices effectively. Leveraging technology, such as advanced analytics and digital tools, can help in integrating QbD by enabling better data collection and analysis, and quality risk management thus supporting decision-making. By embedding QbD principles into existing systems, organisations can build a culture of quality that permeates all aspects of production, leading to improved efficiency, reduced risks, and enhanced product consistency over time.
Tools and Techniques for QbD
Using Risk Assessment Tools
Risk assessment tools are indispensable in the Quality by Design (QbD) framework, providing a structured way to identify and mitigate potential risks in product development. Tools such as Failure Mode and Effects Analysis (FMEA), Hazard Analysis and Critical Control Points (HACCP), and risk matrices help in systematically the process design space evaluating where failures might occur and their potential impact on product quality. By thoroughly analysing process steps and identifying critical control points, these tools enable organisations to prioritise efforts and allocate resources efficiently. Furthermore, risk assessment promotes a proactive approach by highlighting areas that require stringent controls or additional monitoring. This not only safeguards against unforeseen issues but also enhances overall process reliability. Incorporating these tools into the QbD process encourages a deeper understanding of risk dynamics, facilitating more informed decision-making. Ultimately, using risk assessment tools helps ensure that products meet quality standards consistently, thereby supporting regulatory compliance and customer satisfaction.
Leveraging Statistical Methods
Statistical methods are a cornerstone of Quality by Design (QbD), providing robust techniques for understanding product attributes and controlling process variability. Statistical tools such as Design of Experiments (DoE), Statistical Process Control (SPC), and regression analysis enable organisations to explore relationships between variables and optimise processes. By employing DoE, teams can systematically investigate process parameters to identify optimal conditions that yield the desired product quality. SPC techniques, on the other hand, are instrumental in monitoring ongoing production, allowing for the early detection of deviations from set standards. This continuous monitoring ensures processes remain within control limits, thereby maintaining product consistency. Regression analysis aids in predicting outcomes by modelling the impact of multiple factors on quality attributes. Utilising these statistical methods can significantly enhance decision-making by providing data-driven insights, reducing guesswork, and ensuring a scientific approach to quality management. Ultimately, they contribute to achieving a high level of reliability and efficiency in production processes.
Technology in QbD
Technology plays a pivotal role in advancing the principles of Quality by Design (QbD), offering tools and systems that enhance process understanding and control. Automation and digitalisation facilitate real-time monitoring and data acquisition, providing a comprehensive view of manufacturing processes. Technologies such as Process Analytical Technology (PAT) enable in-line quality checks, ensuring that products meet specifications throughout production rather than only at the end. Additionally, advanced data analytics and machine learning algorithms can uncover patterns and correlations that might not be evident through traditional methods. These insights assist in predictive maintenance, reducing downtime and enhancing operational efficiency. Cloud-based solutions and integrated systems improve collaboration across teams, ensuring that data is accessible and actionable. By leveraging such technologies, organisations can implement a more dynamic and responsive approach to quality management, aligning with the core tenets of QbD. This integration supports continuous improvement, leading to higher quality products and more efficient processes.
Overcoming Common Challenges
Addressing Resistance to Change
Resistance to change is a common barrier when implementing Quality by Design (QbD) in organisations. Employees may be hesitant to adopt new methodologies, fearing disruption or increased workloads. To overcome this resistance, clear communication is essential. Leaders should articulate the benefits of QbD, such as improved product quality and reduced errors, demonstrating how these changes align with organisational goals. Involving employees in the transition process can also foster acceptance. By seeking input and feedback, organisations can tailor the QbD approach to better fit current workflows, easing the transition. Training programmes are vital, equipping staff with the necessary skills and confidence to implement QbD principles effectively. Highlighting early successes and quick wins can further bolster support, showcasing the tangible improvements brought by QbD. Ultimately, creating a culture that values continuous improvement and innovation helps embed QbD into the organisation's ethos, ensuring enduring commitment and success.
Ensuring Consistent Quality
Ensuring consistent quality is a fundamental challenge in implementing Quality by Design (QbD). Consistency requires a thorough understanding of the critical quality attributes (CQAs) and the processes that impact them. To achieve this, organisations must develop a robust control strategy that includes comprehensive monitoring and timely adjustments to production variables. Regular audits and evaluations of manufacturing processes help identify areas for improvement, ensuring that any deviations are swiftly addressed. Implementing Statistical Process Control (SPC) tools can facilitate real-time tracking drug evaluation of process performance, allowing for immediate corrective actions. Additionally, fostering a culture of quality within the organisation is crucial. This involves encouraging a mindset where all employees are committed to maintaining high standards and are proactive in identifying and solving quality issues. Training and ongoing education play a vital role in equipping teams with the knowledge and skills needed to uphold these standards. Through these strategies, consistent quality becomes an achievable goal.
Adapting to Regulatory Standards
Adapting to regulatory standards is a significant challenge in implementing Quality by Design (QbD), particularly in highly regulated industries like pharmaceuticals. Regulatory agencies, such as the FDA or EMA, have increasingly endorsed QbD principles, expecting manufacturers to demonstrate a systematic approach to quality management. To align with these expectations, organisations must stay informed about current regulations and guidelines. This requires establishing a dedicated compliance team to interpret and implement regulatory requirements effectively. Integrating regulatory considerations into the QbD framework ensures that all processes are designed and controlled with compliance in mind. Collaboration with regulatory bodies can also provide insights and clarity, fostering smoother approval processes. Documentation is crucial; maintaining thorough records of process development and control strategies helps demonstrate compliance during inspections or audits. By embedding regulatory standards into the QbD approach, organisations can not only meet compliance requirements but also enhance their own quality assurance systems, ultimately benefiting product safety and efficacy.
Future of Quality by Design
Innovations on the Horizon
The future of Quality by Design (QbD) is poised to benefit from several innovative advancements that promise to enhance its implementation. Emerging technologies such as artificial intelligence (AI) and machine learning are set to play pivotal roles in refining QbD processes. These tools can analyse vast datasets to identify trends and predict outcomes, offering unprecedented insights into process optimisation. Additionally, the integration of digital twins—virtual replicas of physical systems—allows for real-time simulation and analysis, facilitating improved process control and reduced development times. Another promising innovation is the use of blockchain for secure and transparent data management, ensuring traceability and integrity throughout the product lifecycle. Advanced sensor technology and the Internet of Things (IoT) are also set to enhance monitoring data analysis capabilities, providing more granular data for quality control. As these technologies mature, they will further embed QbD principles into manufacturing practices, driving efficiency, accuracy, and innovation across industries.
Adapting to Industry Trends
As industries evolve, Quality by Design (QbD) must adapt to emerging trends to remain effective and relevant. One significant trend is the increasing focus on sustainability and eco-friendly manufacturing practices. QbD can incorporate these priorities by emphasising the design of processes raw materials that minimise waste and environmental impact. Additionally, the rise of personalised medicine and customised products demands more flexible and adaptable production processes. QbD frameworks can be adjusted to accommodate these changes by leveraging modular designs and agile methodologies. The digital transformation of industries, driven by advancements in big data and analytics, also influences QbD. By integrating digital tools, organisations can enhance process efficiency and quality control. Moreover, the globalisation of supply chains requires QbD to address diverse regulatory and market demands, ensuring consistent quality across borders. Embracing these industry trends allows QbD to continue delivering value by aligning with broader business objectives and consumer expectations.
QbD in a Global Context
Quality by Design (QbD) is increasingly being adopted in a global context, driven by the need for consistent quality standards across international markets. As businesses expand their reach, they encounter diverse regulatory environments that QbD can help navigate. By providing a structured framework that emphasises process understanding and control, QbD supports compliance with various international standards and regulations. This global applicability makes it a valuable tool for companies operating in multiple regions. Furthermore, QbD fosters harmonisation of quality practices, reducing the complexity and cost associated with meeting different regulatory requirements. Collaboration between regulatory bodies worldwide is also promoting the integration of QbD principles, facilitating smoother approval processes for global companies. Additionally, the global supply chain's complexity necessitates robust quality management systems that QbD can provide, ensuring product consistency pharmaceutical quality and safety across borders. Embracing QbD in a global context not only enhances competitiveness but also contributes to the global standardisation of quality practices.
FAQ
What is Quality by Design (QbD)?
Quality by Design (QbD) is a systematic approach to product development that ensures quality is built into processes from the beginning, reducing risks and improving outcomes.
Why is QbD important in industries like pharmaceuticals?
QbD ensures consistent product quality, safety, and compliance with regulatory standards, which are critical in pharmaceutical manufacturing.
What are the core principles of QbD?
The core principles include understanding product lifecycles, identifying critical quality attributes (CQAs), implementing robust control strategies, and focusing on continuous improvement.
How can organisations implement QbD effectively?
Organisations can implement QbD by identifying key processes, setting measurable objectives, using risk assessment tools, and integrating QbD into existing systems.
What tools are used in QbD implementation?
Common tools include Failure Mode and Effects Analysis (FMEA), Design of Experiments (DoE), Statistical Process Control (SPC), and Process Analytical Technology (PAT).
How does QbD ensure consistent product quality?
QbD employs risk management, process monitoring, and continuous improvement strategies to maintain consistent quality across production cycles.
What challenges are associated with implementing QbD?
Common challenges include resistance to change, adapting to regulatory standards, and ensuring cross-functional collaboration for effective implementation.
How does QbD integrate with regulatory standards?
QbD aligns with guidelines from regulatory bodies like the FDA and EMA, ensuring compliance through systematic quality management and robust documentation.
What role does technology play in QbD?
Technologies like AI, machine learning, digital twins, and IoT enhance process monitoring, data analysis, and predictive quality management in QbD frameworks.
What industries benefit most from QbD?
Industries with strict quality and safety requirements, such as pharmaceuticals, food manufacturing, and biotechnology, benefit significantly from QbD.
How can companies overcome resistance to change when implementing QbD?
Effective communication, staff training, and demonstrating early successes can help overcome resistance to QbD adoption within organisations.
What are critical quality attributes (CQAs) in QbD?
CQAs are the physical, chemical, biological, or microbiological properties that must be controlled to ensure product quality and safety.
How do statistical methods support QbD?
Statistical methods like DoE and SPC help in optimising processes, controlling variability, and ensuring reliable product quality.
What is the role of risk assessment in QbD?
Risk assessment identifies and mitigates potential risks in processes, ensuring robust quality control and reduced variability in outcomes.
What are the future trends in QbD?
Future trends include leveraging AI, blockchain, digital twins, and sustainability-focused designs to enhance QbD practices and outcomes.
How does QbD support sustainability?
QbD encourages efficient processes and minimises waste, aligning with eco-friendly manufacturing and sustainability goals.
Why is continuous improvement essential in QbD?
Continuous improvement ensures processes evolve with technological advancements, regulatory changes, and market demands, maintaining high quality and efficiency.
How does QbD address global market challenges?
QbD provides a consistent framework for quality management, ensuring compliance with diverse regulatory standards and maintaining product consistency across regions.
What is the significance of integrating QbD with existing systems?
Integration ensures that QbD principles enhance current processes, improving overall quality management without disrupting operations.
How does QbD benefit regulatory compliance?
QbD’s structured approach aligns with regulatory requirements, streamlines approvals, and supports thorough documentation for audits and inspections.
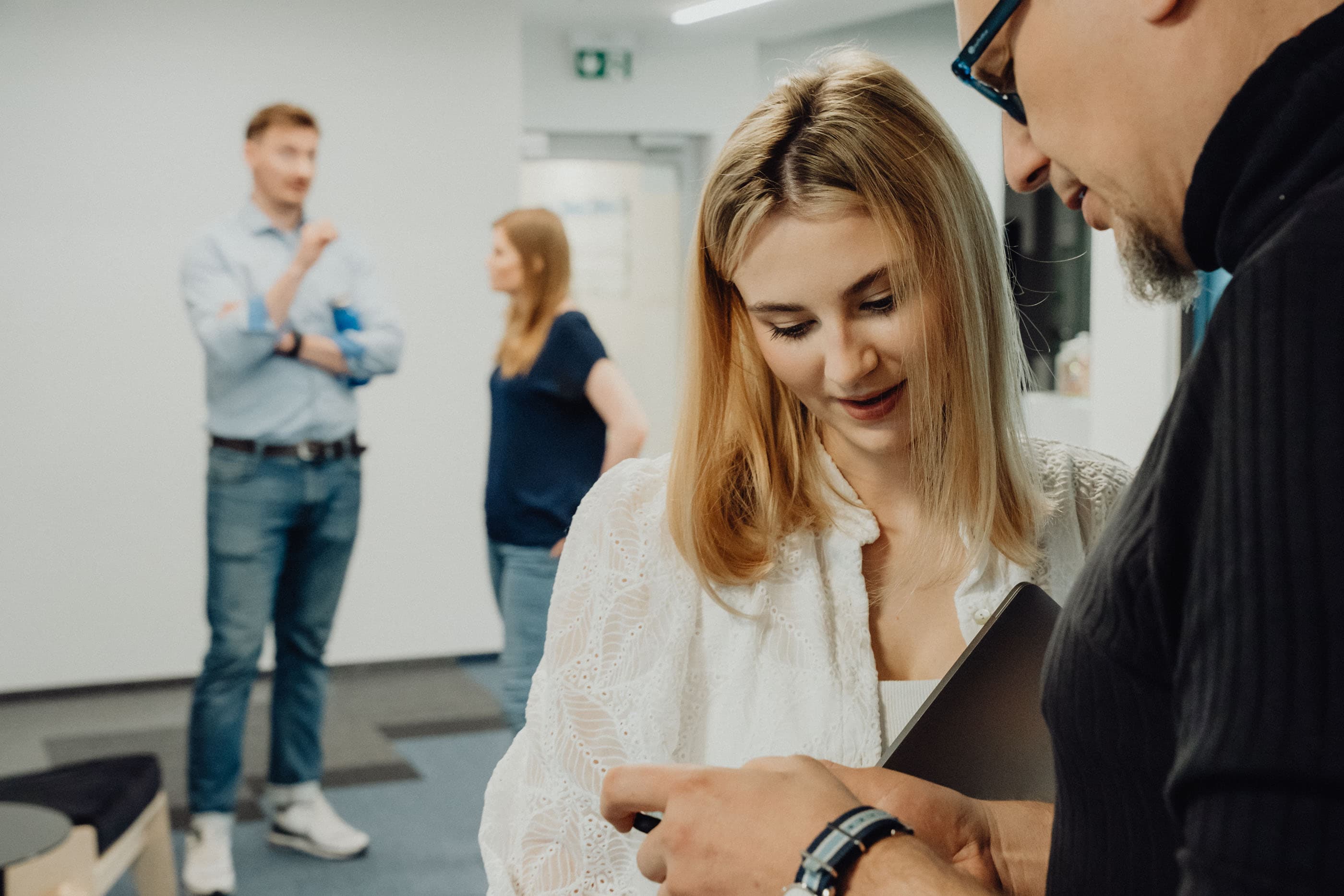
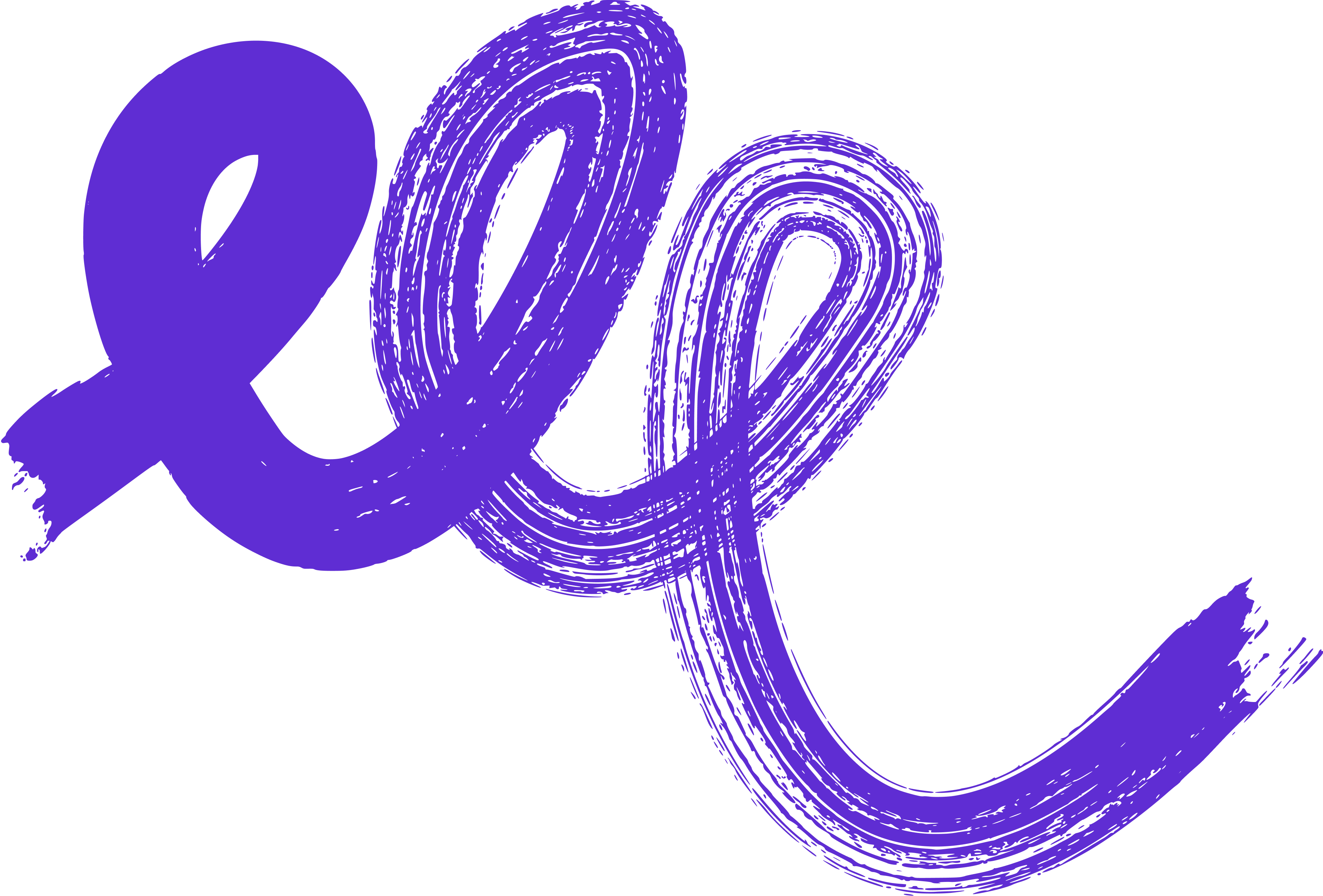
You may also
like...

Turbocharge Your Product Development: Generative AI for Swift Prototyping
Learn how generative AI can transform your prototyping process, delivering faster, more creative, and cost-effective product development.
Alexander Stasiak
Aug 20, 2025・15 min read
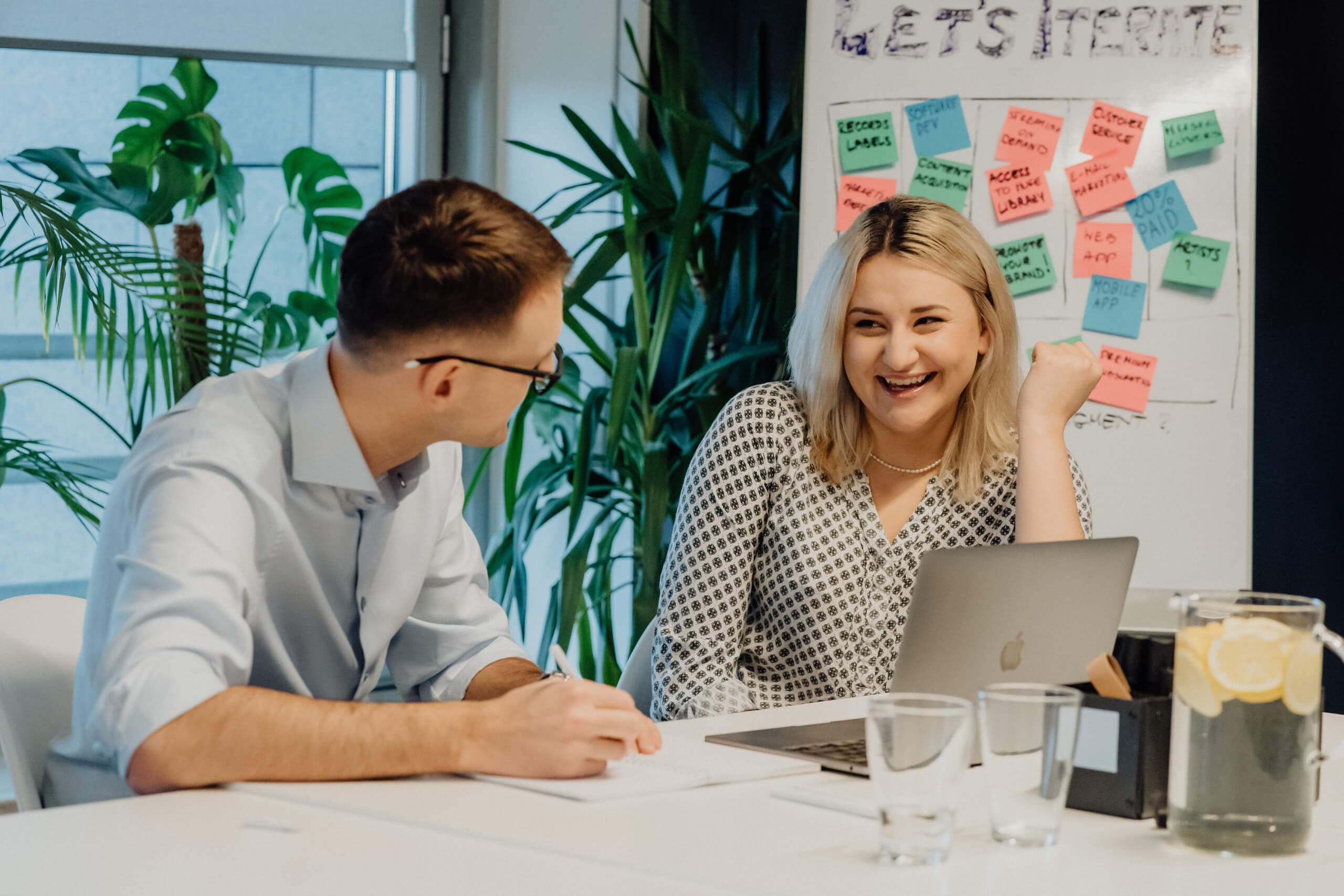
Understanding the Distinctions: Product Design vs Prototype Design Companies
Understanding the difference between product design and prototype design companies can help you choose the right partner at the right stage of product development.
Alexander Stasiak
May 30, 2025・8 min read

Why Choosing the Right Software House Is Crucial for Your Startup’s Success
A great software house can accelerate your startup’s journey from idea to MVP — and beyond. Here’s how to choose the right one.
Alexander Stasiak
Jul 02, 2025・5 min read