🌍 All
About us
Digitalization
News
Startups
Development
Design
Lean vs Six Sigma: Navigating Your Path to Process Improvement
Alexander Stasiak
Dec 06, 2024・8 min read
Table of Content
Understanding Lean and Six Sigma
Benefits of Lean Methodology
Advantages of Six Sigma
Choosing the Right Approach
Real-World Applications
Organisations are constantly seeking ways to enhance their efficiency and quality. Two popular methodologies that have emerged in the realm of process improvement are Lean and Six Sigma. While both aim to streamline operations and reduce waste, they each offer distinct approaches and tools for achieving these goals. the Lean method focuses on removing non-value-added activities to create more flow, whereas Six Sigma targets reducing variation and improving quality through data-driven analysis. In this exploration, we will delve into the principles of Lean and Six Sigma, examining their benefits and helping you determine which path might best suit your organisational needs.
Understanding Lean and Six Sigma
Origins and Key Principles
Lean and Six Sigma, though often intertwined, originate from different backgrounds. Lean has its roots in the Toyota Production System, developed in post-war Japan. The focus was on eliminating waste, or "muda," to improve production efficiency. Its key principles revolve around value creation, streamlining processes, and empowering employees.
On the other hand, Six Sigma was pioneered by Motorola in the 1980s, aiming to improve manufacturing quality by identifying and removing causes of defects and variability. Six Sigma relies heavily on statistical tools and follows a structured methodology, often encapsulated in the DMAIC framework (Define, Measure, Analyse, Improve, Control).
While Lean emphasises speed and efficiency, Six Sigma prioritises precision and consistency. By understanding the origins and principles of these methodologies, organisations can better assess how each might contribute to their process improvement goals.
Fundamental Differences
Lean and Six Sigma differ fundamentally in their approaches to process improvement. Lean focuses on maximising customer value through the relentless elimination of waste. It centres around five core principles: defining value from the customer’s viewpoint, mapping the value stream, creating flow, establishing pull, and seeking perfection. Lean tools include value stream mapping, 5S, and kaizen, which facilitate a culture of continuous improvement.
In contrast, Six Sigma targets reducing process variation and defects. It is highly data-driven and uses statistical analysis to guide decision-making. The methodology is structured around the DMAIC process, which stands for Define, Measure, Analyse, Improve, and Control. Tools used in Six Sigma include process mapping, root cause analysis, and statistical process control.
While Lean aims to improve process speed and efficiency, Six Sigma focuses on process accuracy and predictability. Understanding these fundamental differences helps organisations decide which methodology aligns with their specific improvement goals.
Shared Goals and Techniques
Despite their differences, Lean and Six Sigma share common goals aimed at enhancing process efficiency and quality. Both methodologies strive to improve customer satisfaction by delivering higher quality products and services more efficiently. They focus on reducing waste, albeit in different forms; Lean targets process inefficiencies, while Six Sigma addresses defects and variability.
There are techniques that overlap between the two, such as process mapping and root cause analysis. Both methodologies utilise these tools to gain a comprehensive understanding of processes and identify areas for improvement. Moreover, they rely on employee involvement and a culture of continuous improvement.
Additionally, Lean and Six Sigma both advocate for measuring performance, though Six Sigma is more statistically rigorous. In practice, many organisations find value in integrating both methodologies, creating a lean Six Sigma approach that leverages the strengths of each to achieve more holistic process improvements. This synergy can drive significant operational excellence.
Benefits of Lean Methodology
Eliminating Waste
A core benefit of Lean methodology is its focus on eliminating waste, which it categorises into seven types: overproduction, waiting, transport, extra processing, inventory, motion, and defects. By targeting these, Lean aims to streamline operations, reduce costs, and enhance overall efficiency.
Companies adopting Lean techniques often employ tools like 5S and value stream mapping to identify and remove non-value-added activities. This leads to more efficient workflows, as processes are designed to add maximum value from the customer’s perspective.
Furthermore, by fostering a culture of continuous improvement and employee empowerment, Lean encourages team members to actively seek out inefficiencies and propose solutions. This participatory approach not only boosts morale but also ensures that improvements are sustainable over time.
By removing unnecessary steps process complexity and focusing on what truly adds value, organisations can achieve faster production times and increased flexibility, crucial in today’s competitive market.
Enhancing Efficiency
Lean methodology significantly enhances efficiency by focusing on optimising processes to deliver value swiftly and effectively. By implementing Lean principles, organisations can further streamline processes and workflows, thus reducing lead times and increasing throughput. This efficiency gain is achieved through practices like just-in-time production, which ensures that resources are used only as needed, reducing inventory costs and minimising waste.
The emphasis on creating smooth process flow is another aspect that boosts efficiency. Lean encourages the elimination of bottlenecks and interruptions, which can often slow down production and lead to inefficiencies. By maintaining a steady flow, tasks are completed quicker and more reliably, contributing to overall operational excellence.
Moreover, by empowering employees to identify and rectify inefficiencies, Lean fosters a proactive work environment where continuous improvement is the norm. This not only supports efficiency but also drives innovation and adaptability, enabling organisations to respond swiftly to market changes and customer demands.
Improving Customer Satisfaction
Lean methodology directly contributes to improving customer satisfaction by aligning processes with customer needs and expectations. By focusing on value from the customer's perspective, Lean ensures that every step in the production process enhances the final product's quality and relevance. This customer-centric approach leads to products and services that better meet customer demands, thereby increasing satisfaction levels.
The methodology's emphasis on reducing waste and improving efficiency means that products can be delivered faster and with greater consistency. Timely delivery and reliable quality are crucial factors that influence customer satisfaction. By minimising defects and ensuring products are right the first time, Lean reduces the likelihood of customer complaints and returns.
Moreover, Lean fosters an organisational culture that is responsive and adaptable to customer feedback. By continually seeking ways to improve and innovate, businesses can better anticipate and fulfil customer needs, thereby strengthening relationships and securing long-term loyalty.
Advantages of Six Sigma
Reducing Variation
Six Sigma's primary strength lies in its ability to reduce variation within processes, thereby enhancing product quality and consistency. By employing statistical tools and techniques to reduce process variation, Six Sigma identifies the root causes of variation and implements solutions to minimise deviations. This systematic approach ensures that processes are predictable and operate within strict quality standards.
The methodology's structured framework, DMAIC (Define, Measure, Analyse, Improve, Control), provides a disciplined process for tackling variation. Each phase of DMAIC is designed to delve deeper into understanding the process and uncovering areas where variability can be reduced. This results in processes that consistently produce high-quality outputs, meeting or exceeding customer expectations.
Reducing variation not only improves product quality but also leads to cost savings. With fewer defects and rework, organisations can lower operational costs and increase efficiency. Furthermore, consistent quality enhances customer trust and loyalty, as they can rely on receiving products that meet their specifications every time.
Data-Driven Decision Making
Six Sigma emphasises data-driven decision making, which is pivotal in ensuring accurate and reliable business process improvements. By relying on empirical evidence and statistical analysis, Six Sigma removes guesswork from decision-making processes, allowing organisations to make informed choices that are based on actual data rather than assumptions.
The use of data in Six Sigma begins with the Define and Measure phases of the DMAIC process, where data is collected to understand current processes and performance levels. In the Analyse phase, this data is thoroughly examined to identify trends, patterns, and root causes of defects. This analytical approach ensures that solutions are tailored to the specific issues impacting quality.
By basing decisions on concrete data, Six Sigma helps organisations implement changes that lead to measurable improvements in performance. This robust framework reduces the risk of errors and enhances overall process efficiency. Moreover, a culture of data-driven decision making fosters transparency and accountability, contributing to sustained organisational growth and excellence.
Boosting Quality Control
Six Sigma significantly enhances quality and control processes by implementing rigorous standards and robust methodologies to monitor and maintain quality throughout processes. This approach ensures that products and services consistently meet high-quality benchmarks, thereby reducing the incidence of defects and rework.
Key to Six Sigma’s success in quality control is its focus on identifying and eliminating the root causes of defects. By employing tools such as Statistical Process Control (SPC) and Failure Mode and Effects Analysis (FMEA), Six Sigma practitioners can detect potential for quality management issues before they escalate, allowing for preemptive corrective actions.
The methodology’s structured approach, particularly through the Control phase of DMAIC, ensures that improvements are sustained over time. By establishing control plans and continuous monitoring, organisations can maintain the enhanced quality levels achieved through Six Sigma initiatives.
This heightened emphasis on quality control not only satisfies customer expectations but also enhances organisational reputation, leading to increased competitiveness in the market.
Choosing the Right Approach
Assessing Organisational Needs
Before deciding between Lean and Six Sigma, organisations must thoroughly assess their specific needs and objectives. This evaluation involves understanding the current challenges faced by the organisation, such as inefficiencies, high defect rates, or customer satisfaction issues. Pinpointing these problems helps in determining which methodology might offer the most effective solutions.
Organisations should consider the nature of their processes and products. For industries with complex processes and high variability, Six Sigma's data-driven approach may be more beneficial. Conversely, if the primary goal is to improve speed and eliminate waste, Lean principles could be more effective.
It is also crucial to evaluate the organisational culture and readiness for change. Lean requires a collaborative environment and continuous employee involvement, whereas Six Sigma demands a commitment to rigorous data analysis and statistical analysis. By aligning the choice of methodology with organisational goals and culture, businesses can ensure a more successful implementation and achieve significant improvements in efficiency and quality.
Combining Lean and Six Sigma
For many organisations, combining Lean and Six Sigma offers a comprehensive approach to process improvement. This hybrid, often referred to as Lean Six Sigma, leverages the strengths of both methodologies to maximise efficiency and quality. By integrating Lean's waste reduction techniques with Six Sigma's focus on reducing variation, organisations can achieve more holistic improvements.
Lean Six Sigma provides a flexible framework that can be tailored to address a wide range of challenges. It encourages a balanced approach, where efficiency and quality are both prioritised. This combination can lead to streamlined operations, improved production times, and enhanced product quality.
Implementing Lean Six Sigma requires a commitment to both methodologies' principles and tools. Organisations need to invest in training and development to equip employees with the skills necessary to apply Lean Six Sigma effectively. By fostering a culture of continuous improvement and data-driven decision-making, businesses can achieve sustainable growth and competitive advantage in a rapidly changing market.
Implementing Change Successfully
Successfully implementing Lean, Six Sigma, or a combined approach requires careful planning and execution. The first step is securing buy-in from leadership and creating a shared vision for the change. Leaders must communicate the benefits and objectives clearly to ensure alignment and motivation across the organisation.
Organisations should develop a structured change management plan that includes training, resource allocation, and timelines. Investing in employee training is critical, as it equips teams with the knowledge and skills needed to apply Lean and Six Sigma tools effectively.
It's essential to foster a culture of collaboration and open communication. Encouraging employee involvement and feedback throughout the implementation process can identify potential issues early and promote a sense of ownership and engagement.
Finally, measuring and tracking progress regularly is crucial for sustaining change. By using key performance indicators (KPIs) to monitor improvements, organisations can ensure that the benefits of Lean and Six Sigma are realised and maintained over the long term.
Real-World Applications
Case Studies of Lean
Lean methodology has been successfully applied across various industries, yielding impressive results. In the automotive sector, Toyota is a prominent example, having utilised Lean principles to streamline its production processes. By focusing on waste elimination and continuous improvement, Toyota enhanced its manufacturing efficiency, reduced costs, and improved product quality, setting a benchmark for others in the industry.
In healthcare, Lean has been instrumental in improving patient care and reducing waiting times. For instance, Virginia Mason Medical Center in Seattle adopted Lean principles to redesign its clinical processes. This implementation led to significant improvements in patient flow, increased staff productivity, and enhanced patient satisfaction.
Manufacturing giant Textron, known for its aviation and defence products, also embraced Lean. By focusing on value stream mapping and waste reduction, Textron achieved shorter lead times and improved inventory management.
These case studies highlight Lean’s versatility and effectiveness in driving operational excellence and delivering value to customers across diverse sectors.
Successful Six Sigma Implementations
Six Sigma has been effectively utilised by numerous organisations to enhance quality and operational efficiency. One notable example is General Electric, which adopted Six Sigma in the 1990s under CEO Jack Welch. By focusing on defect reduction and process optimisation, GE achieved significant cost savings and quality improvements across its diverse business units.
In the financial services sector, Bank of America implemented Six Sigma to improve customer service and streamline operations. The bank used data-driven analysis to identify and address process inefficiencies, resulting in enhanced customer satisfaction and reduced operational costs.
Motorola, the original pioneer of Six Sigma, achieved remarkable success by applying the methodology to its manufacturing processes. Through rigorous statistical analysis and process improvements, Motorola significantly reduced defects, leading to higher product quality and increased market competitiveness.
These successful implementations underscore Six Sigma’s power to drive substantial improvements in quality and efficiency across different industries, proving its value as a strategic tool for business excellence.
Hybrid Models in Practice
Hybrid models that combine Lean and Six Sigma have been adopted by many organisations seeking comprehensive process improvement strategies. Lean Six Sigma integrates Lean's efficiency-focused methods with Six Sigma's emphasis on quality and defect reduction, offering a balanced approach to operational excellence.
For instance, 3M effectively utilised Lean Six Sigma to streamline its production processes and boost product quality. By reducing waste and variability, 3M achieved faster production cycles and enhanced customer satisfaction, leading to significant cost savings.
In healthcare, the NHS in the UK has implemented Lean Six Sigma to improve patient care and optimise resource utilisation. By applying this hybrid model, NHS hospitals have reduced patient wait times and improved service delivery, showcasing the methodology's adaptability to complex systems.
These examples demonstrate how hybrid models can provide organisations with the flexibility and tools needed to address both efficiency and quality challenges, resulting in sustainable improvements and competitive advantages.
FAQ
What is the difference between Lean and Six Sigma?
Lean focuses on eliminating waste and improving efficiency, while Six Sigma targets reducing process variation and defects through data-driven analysis.
What are the origins of Lean and Six Sigma?
Lean originates from the Toyota Production System, emphasising waste elimination. Six Sigma was developed by Motorola to improve quality through statistical methods.
How do Lean and Six Sigma achieve process improvement?
Lean achieves improvement by streamlining workflows and removing non-value-added activities, while Six Sigma improves quality by identifying and reducing variation.
What are the benefits of Lean methodology?
Lean enhances efficiency by eliminating waste, improves process flow, and aligns operations with customer needs, leading to higher satisfaction.
What are the benefits of Six Sigma?
Six Sigma reduces variation, boosts quality control, and promotes data-driven decision-making, ensuring consistent results and fewer defects.
What are the seven types of waste in Lean?
The seven types of waste are overproduction, waiting, transport, extra processing, inventory, motion, and defects.
What is the DMAIC framework in Six Sigma?
DMAIC stands for Define, Measure, Analyse, Improve, and Control—a structured process for identifying and eliminating defects.
What tools are used in Lean methodology?
Lean tools include value stream mapping, 5S, kaizen (continuous improvement), and just-in-time production.
What tools are used in Six Sigma?
Six Sigma tools include Statistical Process Control (SPC), root cause analysis, Failure Mode and Effects Analysis (FMEA), and process mapping.
Can Lean and Six Sigma be used together?
Yes, Lean Six Sigma combines Lean's efficiency with Six Sigma's quality control to create a comprehensive process improvement approach.
How do I decide between Lean and Six Sigma?
Assess your organisational needs: Lean suits businesses focusing on speed and waste reduction, while Six Sigma is ideal for reducing variation and improving quality.
What industries benefit from Lean methodology?
Lean is widely used in manufacturing, healthcare, logistics, and services to streamline workflows and improve efficiency.
Which industries use Six Sigma?
Six Sigma is popular in manufacturing, finance, healthcare, and technology sectors where quality control and precision are critical.
What is Lean Six Sigma?
Lean Six Sigma combines the principles of Lean (waste elimination) and Six Sigma (variation reduction) to enhance both efficiency and quality.
How does Lean improve customer satisfaction?
Lean aligns processes with customer needs, reduces lead times, and delivers consistent, high-quality products or services.
How does Six Sigma ensure quality control?
Six Sigma uses statistical analysis to identify root causes of defects and implements solutions to ensure consistent, high-quality outcomes.
What are some real-world examples of Lean implementation?
Toyota, Virginia Mason Medical Center, and Textron have successfully used Lean to reduce waste, improve workflows, and enhance customer satisfaction.
What are successful examples of Six Sigma in action?
General Electric, Motorola, and Bank of America used Six Sigma to reduce defects, improve processes, and achieve significant cost savings.
How can Lean Six Sigma benefit an organisation?
Lean Six Sigma integrates waste reduction and quality control, providing a balanced framework for achieving operational excellence.
What are the challenges of implementing Lean or Six Sigma?
Challenges include securing leadership buy-in, fostering a culture of continuous improvement, and ensuring proper employee training and engagement.
What is the role of data in Six Sigma?
Data drives decision-making in Six Sigma, ensuring changes are based on statistical evidence rather than assumptions.
How can organisations measure the success of Lean or Six Sigma?
Success can be measured through key performance indicators (KPIs) such as cost reduction, defect rates, cycle time improvement, and customer satisfaction scores.

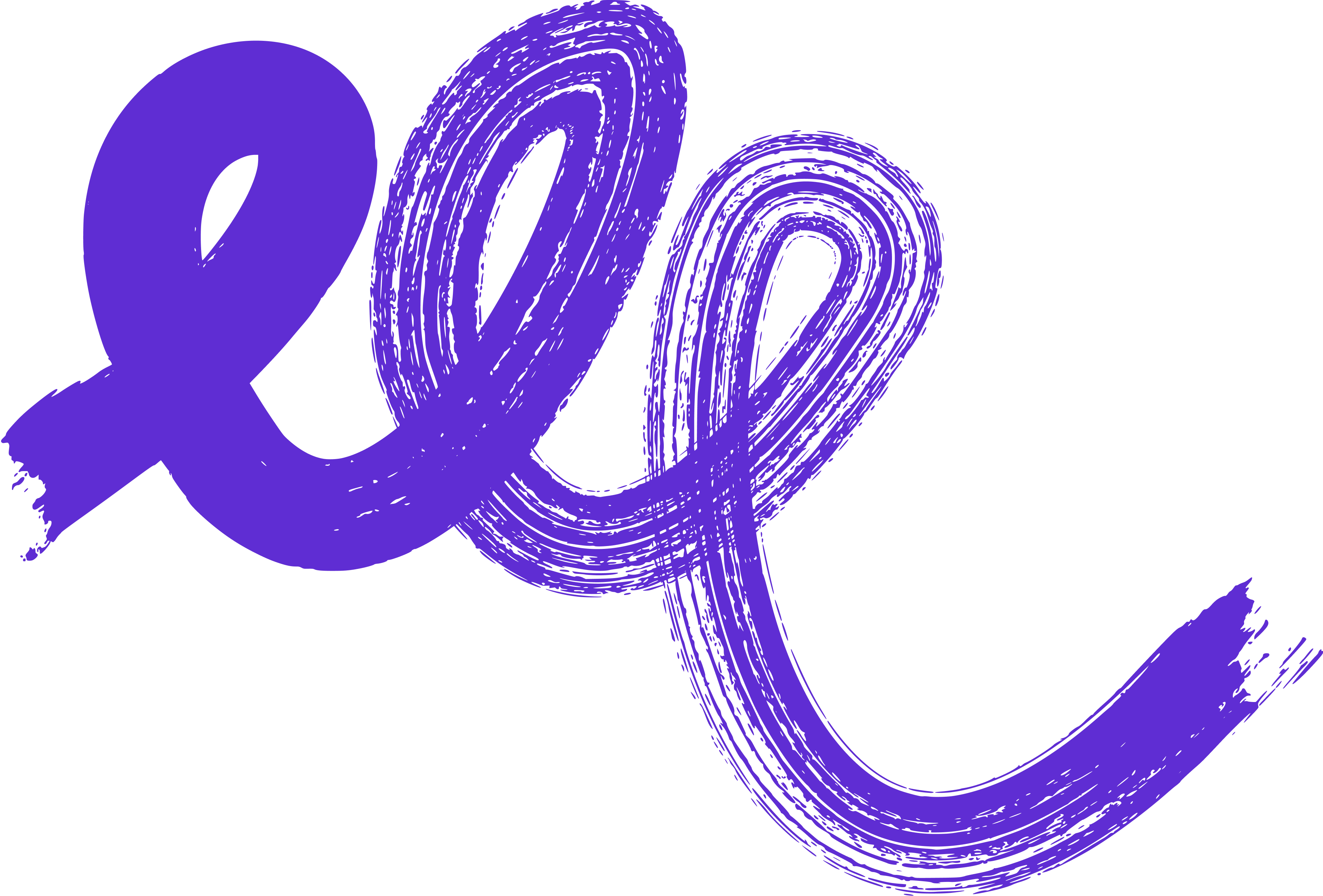
You may also
like...

Mastering the Art of RFPs: A Practical Guide for Software Development Projects
A step-by-step guide to writing clear, effective RFPs that attract the right vendors and drive successful software projects.
Alexander Stasiak
Feb 19, 2025・13 min read
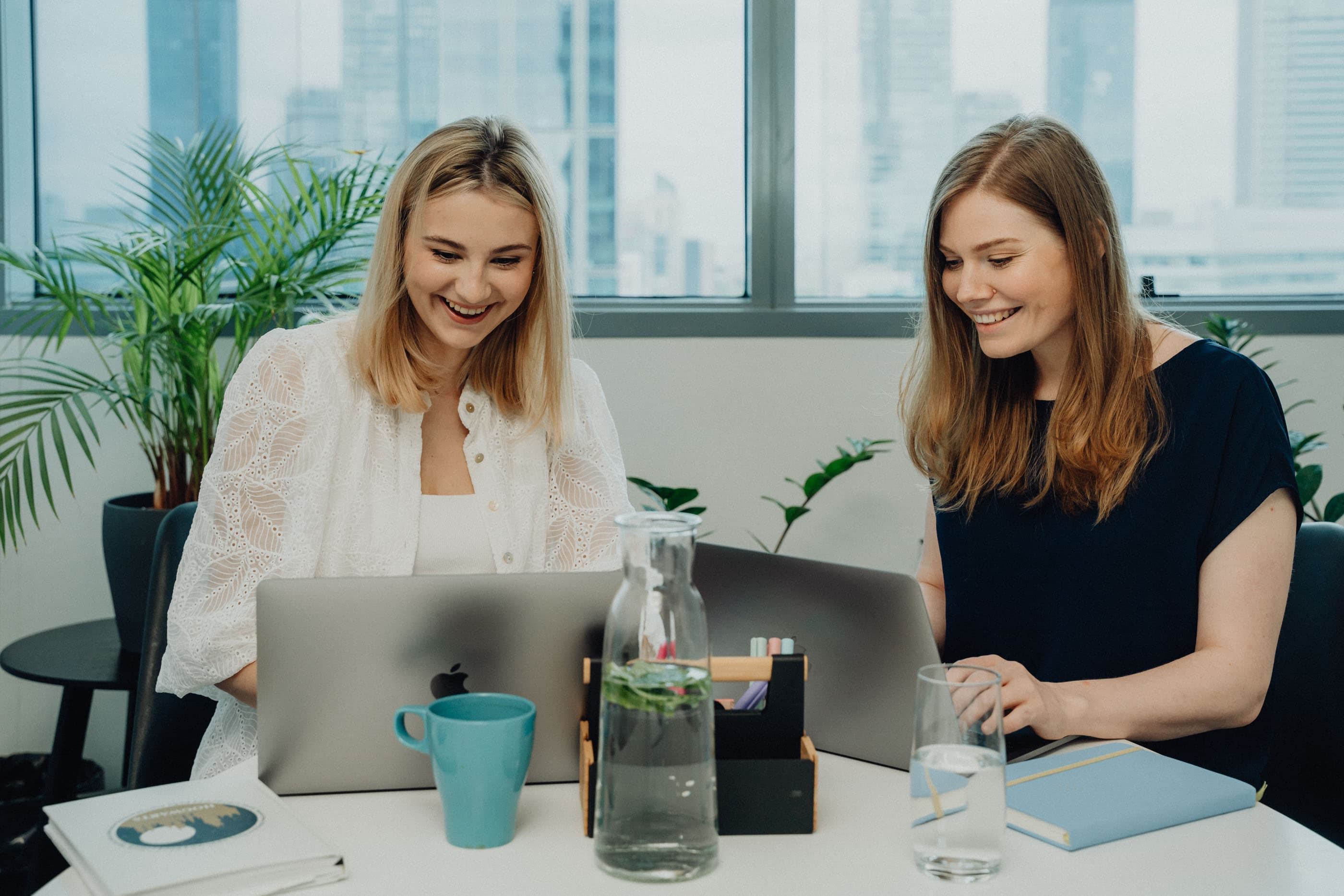
Mastering Declarative Programming: Essential Practices for Every Developer
Discover declarative programming essentials. This guide covers principles, tools, and best practices to simplify coding, enhance readability, and improve scalability.
Marek Pałys
Apr 16, 2024・11 min read
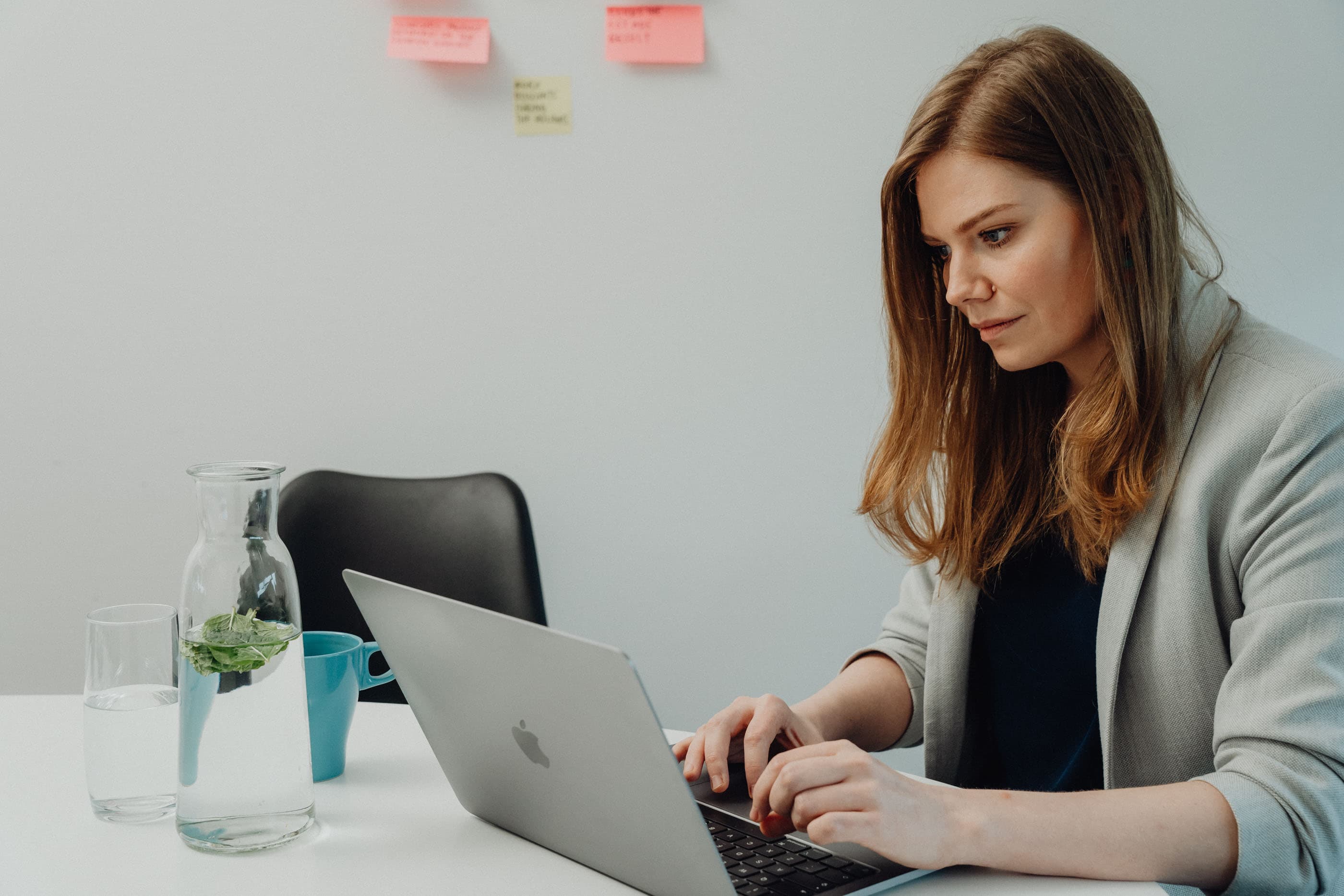
Understanding Event-Driven Programming: A Simple Guide for Everyone
Explore the essentials of event-driven programming. Learn how this responsive paradigm powers interactive applications with real-world examples and key concepts.
Marek Pałys
Apr 30, 2024・9 min read